High Density Propulsion Technologies for Small Satellites: Propellant and Thruster
Student: Morgan A. Roddy
Degree: Ph.D., July 2020
Major Professor: Dr. Adam Huang
Research Area(s):
Microelectonics
Photonics
Background/Relevance
- Small Satellites must store propellant as dense as possible for optimal capability.
- Compact and reliable thruster architectures for are needed for deep-space exploration
Innovation
- Use solid-subliming materials to etch high density materials to generate propellant.
- Use LTCC to integrate all elements of an electrostatic thruster into a single monolithic structure for enhanced thruster lifetime.
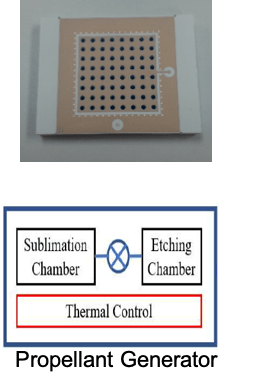
Approach
- Let xenon difluoride (XeF2) sublimate at a rate controlled by chamber pressure.
- Etch tungsten (W) with XeF2 vapor.
- Use W and XeF2 reaction products as a propellant.
- Built up layers of ceramic material with voids embedded conductors to realize internal cavities and wiring.
- Test prototypes by investigating the RF power required to ignite a plasma as a function of propellant flow rate.
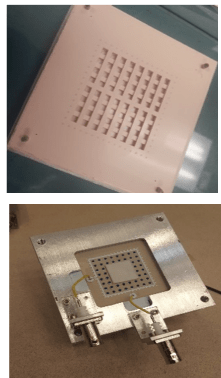
Key Results
- Demonstrated ‘best-in-class’ propellant storage density, 5.2g/cc
- Successfully fabricated 3 prototypes of the Low-Temperature Cofired Ceramic Electrostatic Thruster (LTCC-ET) at the UofA.
- Conducted plasma ignition testing at the Pulsed Power Plasma Diagnostics Laboratory at NASA’s Marshall Space Flight Center.

Conclusions
- Subliming etching material can be used to convert a wide range of materials into a propellant stream.
- Etchant recovery would enable the use of non-standard propellant in perpetuity, such as regolith or asteroid materials.
- The LTCC-ET could be evolved to realize a self neutralizing and thrust vectoring propulsion system for interplanetary exploration.
Future Work
- Prototype and optimize an integrated propellant generator.
- Optimize the thruster’s electrical, mechanical, and thermal design.